Joint Improvement Programme
Disruptive approach to (production) process improvements
A site scan to analyse existing production processes and make immediate, concrete improvement proposals to industrial players is the latest form of service provided by ERIKS. The Joint Improvement Program - or JIP - is a tailor-made programme in which our experts identify bottlenecks in your company, carry out analyses, spar with you and your employees, and then come up with a well-founded recommendation that will save you money.
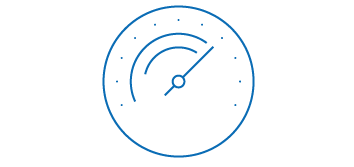
JIP | Focus on optimisation
Such well-substantiated advice from the JIP team in the form of concrete improvement proposals focuses on optimising your business processes and making them more sustainable, and - where possible - using innovative techniques.
Themes that are central to site scans:
- Overall Equipment Effectiveness [OEE]
- Process Efficiency
- Quality
- Energy savings (CO2)
- Safety and Environment
In order to gain insight into these issues for you, ERIKS uses proven methods such as Scrum and Agile.
4 steps to improvement proposals
The Joint Improvement Programme consists of four different phases, namely: 1. Context | 2. Ideation | 3. Prototype | and 4. Pitch
Phase 1 | Context
The first phase is context. As much data as possible is collected. Then, together with you, we determine the areas of attention. Where do problems regularly occur, is there downtime and why, are there leaks or are there safety issues?
The ERIKS team consists of experienced Application Engineers who are highly knowledgeable about the components, applications and processes we encounter in flow technology, power transmission, sealing technology, maintenance and safety. This team has short conversations with as many people as possible, from operators to the plant manager, based on the idea: 'you can only make improvements by really listening'.
Phase 2 | Ideation
During the ideation phase, all information from the discussions is brought together. In a kind of 'war room' at your location, all problems, processes, bottlenecks and comments are recorded and made clear. The team brings structure to the chaos. The biggest pain points per process are mapped out. The team will also discuss the possible solutions with your employees.
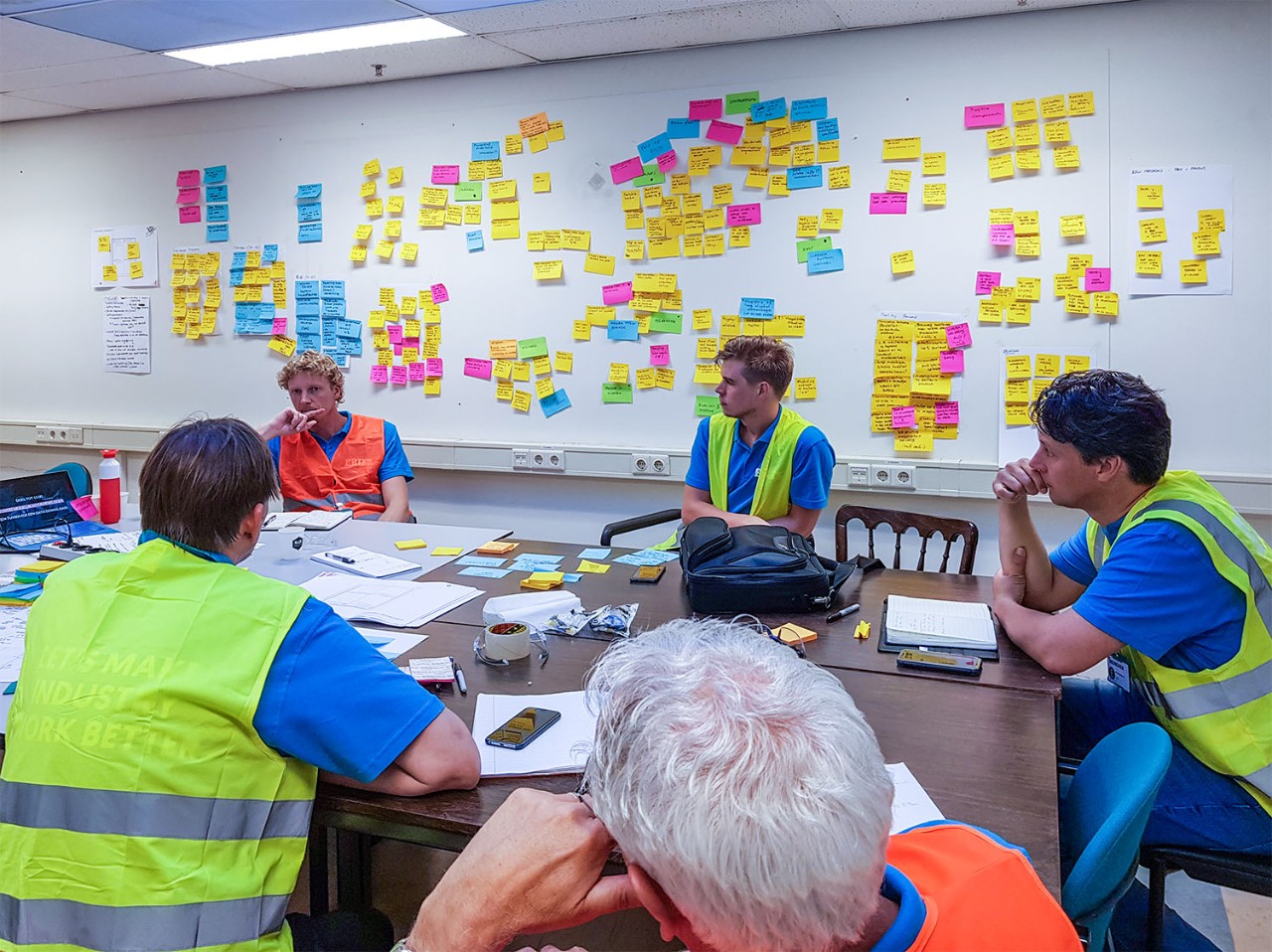
"Only by really listening,
is when you can make improvements."
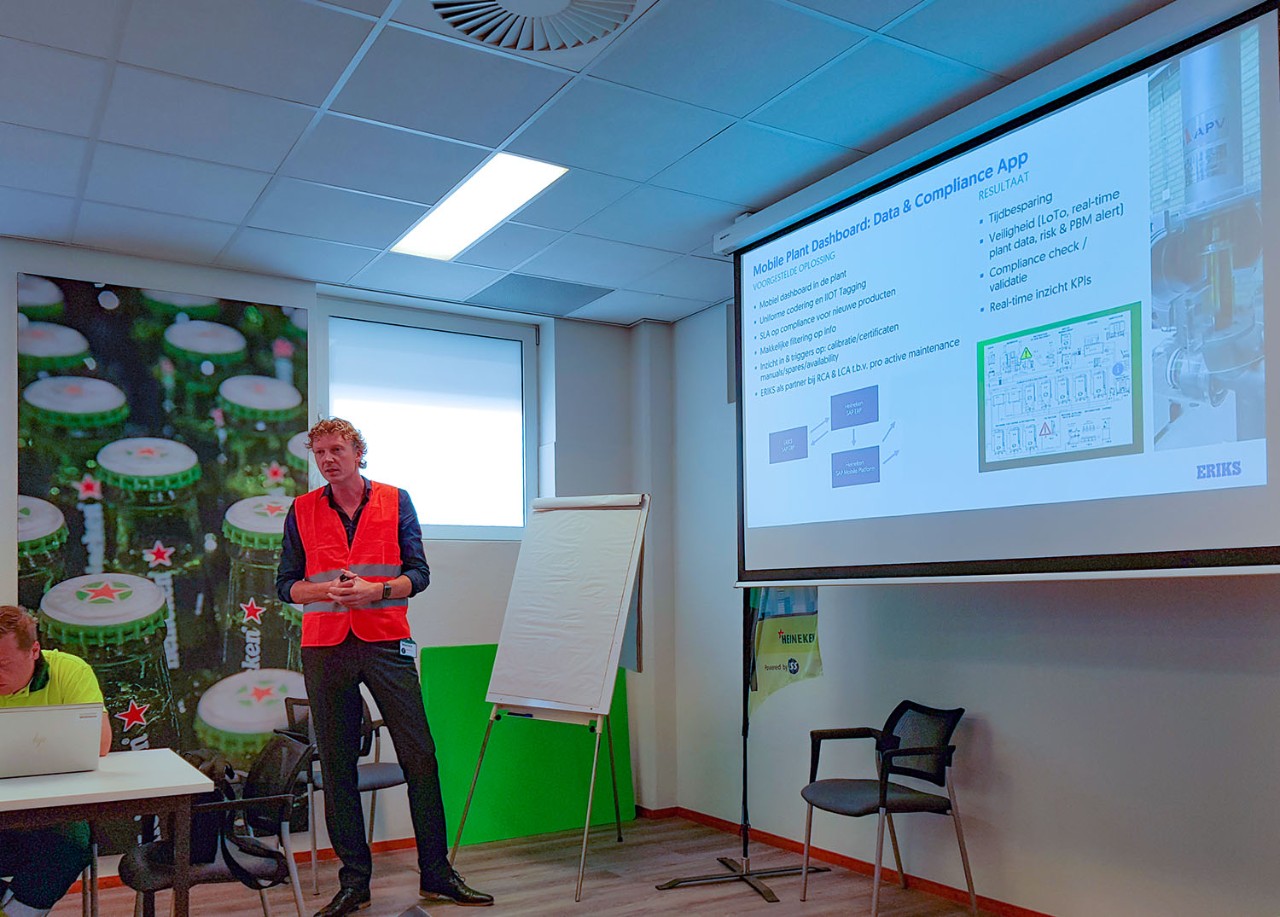
Phase 3 | Prototype
Now the JIP team gets to work with all the resulting ideas and insights. By means of presentations, drawings and prototypes, it is made clear to you how the solutions can be applied in practice. In doing so, we always check whether the desired direction is in line with your wishes. We regularly go back into the factory to hear whether we are on the right track.
Phase 4 | Pitch
Finally, the solutions are presented to you during a pitch. We show the problems identified, present prototypes and solutions and demonstrate the savings that are possible. This can vary from more energy-efficient motors, the replacement of a valve to the optimisation of a complete production. You then decide which solutions you would like to see and prioritise for your company, and how they will be followed up.
JIP | From signalling to implementation of improvements
The advantage of the JIP session is that our helicopter view gets us to the core of all kinds of bottlenecks in a very short time. It costs you and your colleagues little time and we are quickly able to arrive at quantifiable savings and solutions.
ERIKS is happy to help you implement and monitor the improvements. In terms of approach, JIP is the ultimate translation of our mission 'Let's make industry work better'.
More information
Are you curious what JIP can do for your company? Challenge us and contact us for an informal talk.
T +31 88 855 90 62
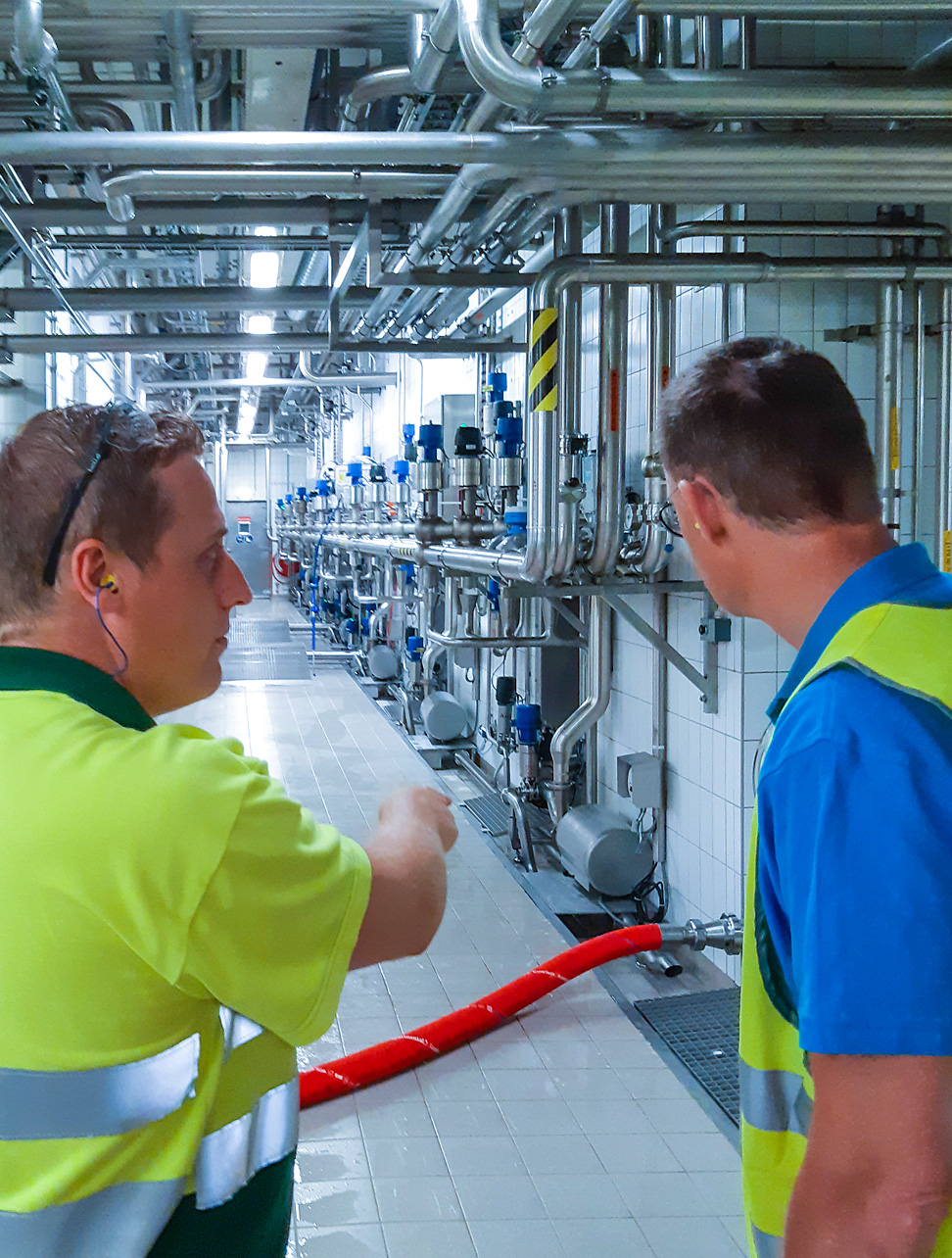
JIP in practice | Heineken
As a strategic partner of Heineken, ERIKS was keen to carry out the Joint Improvement Program at this company of its name. It was a pleasure to work with them. Heineken has, of course, already organised a lot well, with a technical department of 100 people including many specialists.
Peter Oosterveld, Manager Innovations & Investments of the Heineken location in Den Bosch was surprised that ERIKS could gather so much knowledge about the company and its processes in such a short time.
Watch the whole interview about his experience with the ERIKS JIP.
Onze services voor maatwerk
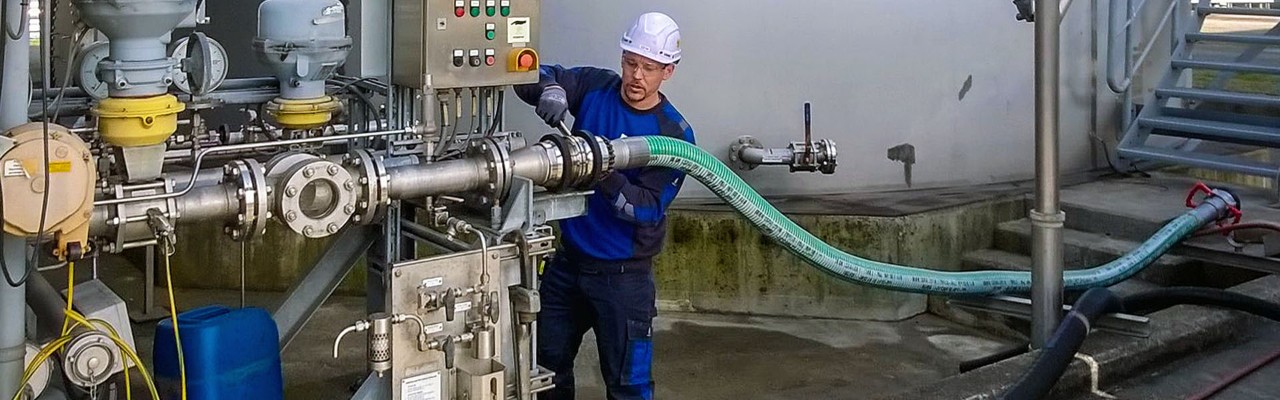
Slang inspecties on-site
Tijdens regulier gebruik van uw slangen worden deze blootgesteld aan verschillende invloeden. Slijtage kan een veiligheidissue veroorzaken. Om ervoor te zorgen dat uw slangen blijvend veilig zijn voor gebruik, kunt u ze door ERIKS on-site laten inspecteren. Wij beperken de down-time zo tot een minimum.
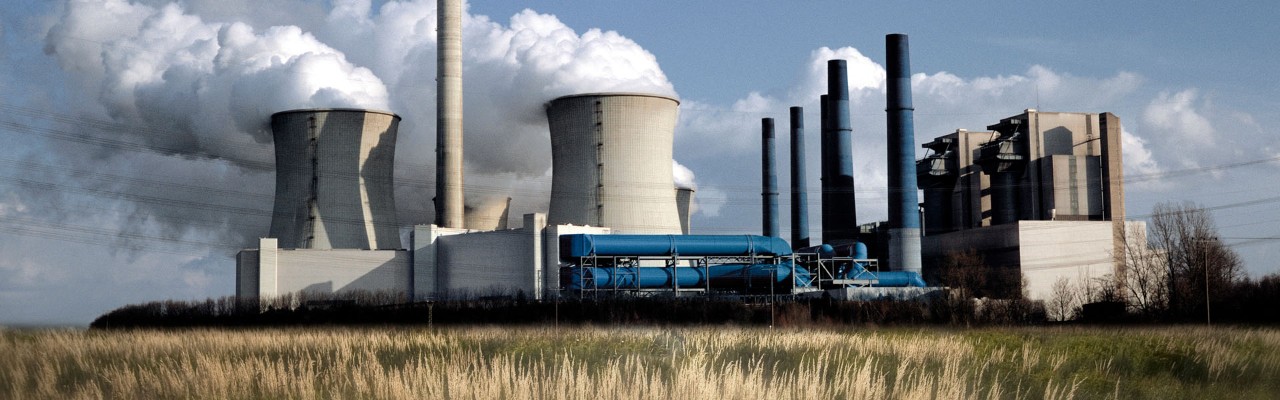
Energiebesparende oplossingen
U wilt uw energieverbruik verminderen? Minder energie betekent lagere kosten en ook minder CO2-uitstoot. ERIKS verzorgt complete quick scans om onderzoek te doen naar energieverspilling en potentiële besparingen binnen uw bedrijf. Na een rapportage, gaan wij tot actie over.
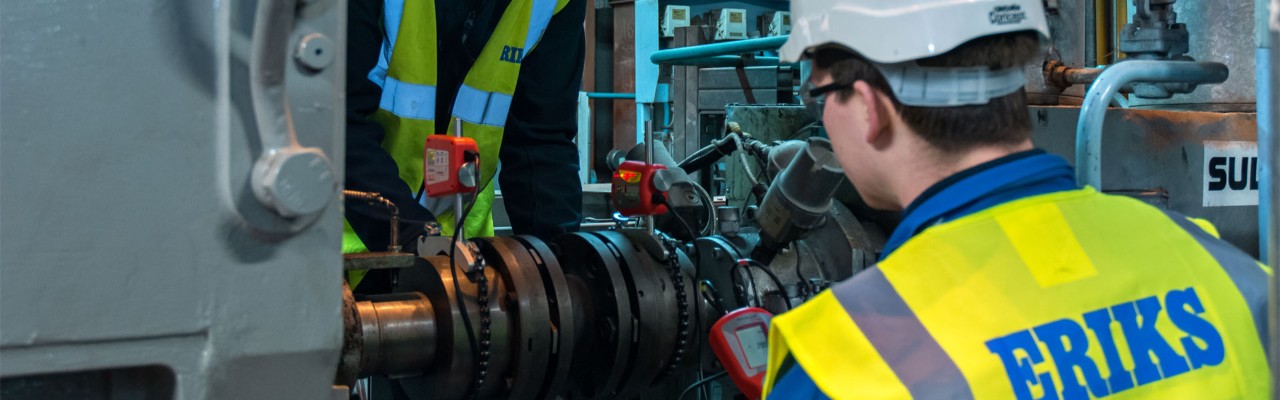
Monitoring & inspectie
Stel je een fabriek voor met assets die altijd in topconditie zijn, reparaties en onderhoud zijn van tevoren gepland en de productie is altijd optimaal. Bij ERIKS maken onze voorspellende en preventietechnieken vroegtijdige waarschuwingen mogelijk, ruim voordat de situatie kritiek wordt. Daarmee voorkomt u onverwachte downtime.
How to Contact ERIKS
Get in Touch
Looking for a custom Product quote? Need an answer to a Technical question? Looking for Careers/HR support? Want to work with us? Interested in our Digital Trading solutions? Have a finance question? Send us your enquiry and a member of the ERIKS team will be with you quickly.
How are we doing?
We strive to deliver exceptional quality service and products. As part of this goal, we encourage customers to submit feedback on their experiences so we can resolve any issues and concerns.
Call us or find your local Branch
At ERIKS we strive to deliver the best quality service and products. As part of this goal we encourage customers to submit feedback on their experiences so we can resolve any issues and concerns.
Call us: +441215086000
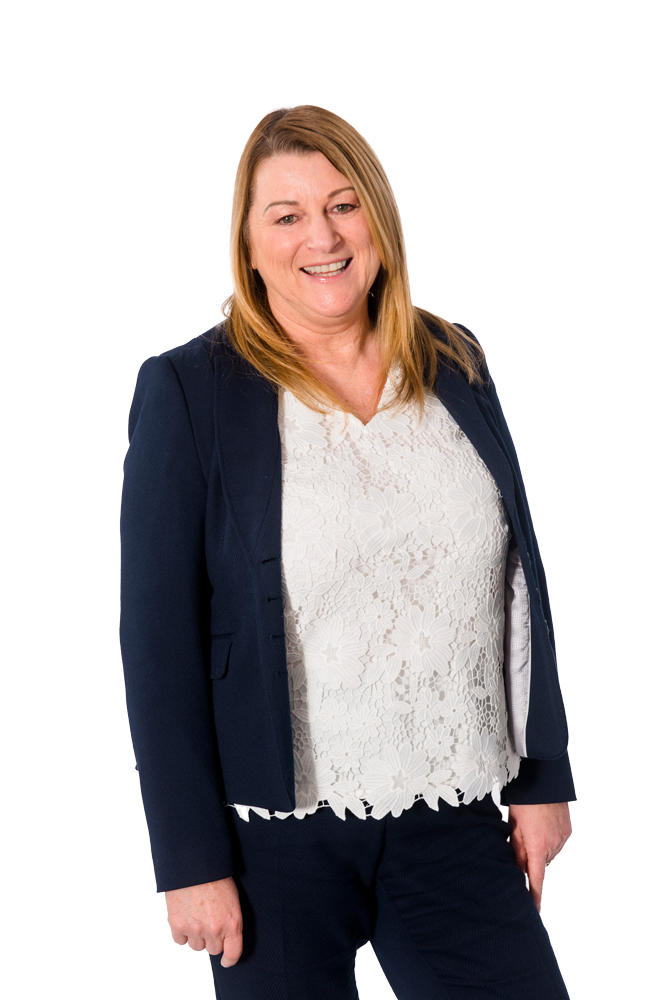