Facilities Management Problem Solvers
Quick Wins for Facilities Management
From a flowmeter to a quick fix belt we have a number of little solutions which deliver large benefits including reduced downtime, increased production, improved health and safety amongst a number of other efficiencies.
Take a look at the problems below, if any of them sound familiar you're one click away from the solution!
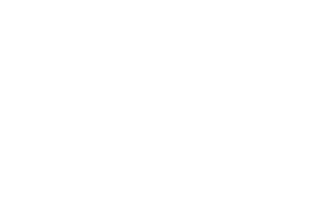
More Coming Soon... Don't Forget to Check Back!
This page is regularly updated with the latest Problem Solvers as new technologies, products and innovations are introduced.
How to Contact ERIKS
Get in Touch
Looking for a custom Product quote? Need an answer to a Technical question? Looking for Careers/HR support? Want to work with us? Interested in our Digital Trading solutions? Have a finance question? Send us your enquiry and a member of the ERIKS team will be with you quickly.
How are we doing?
We strive to deliver exceptional quality service and products. As part of this goal, we encourage customers to submit feedback on their experiences so we can resolve any issues and concerns.
Call us or find your local Branch
At ERIKS we strive to deliver the best quality service and products. As part of this goal we encourage customers to submit feedback on their experiences so we can resolve any issues and concerns.
Call us: +441215086000
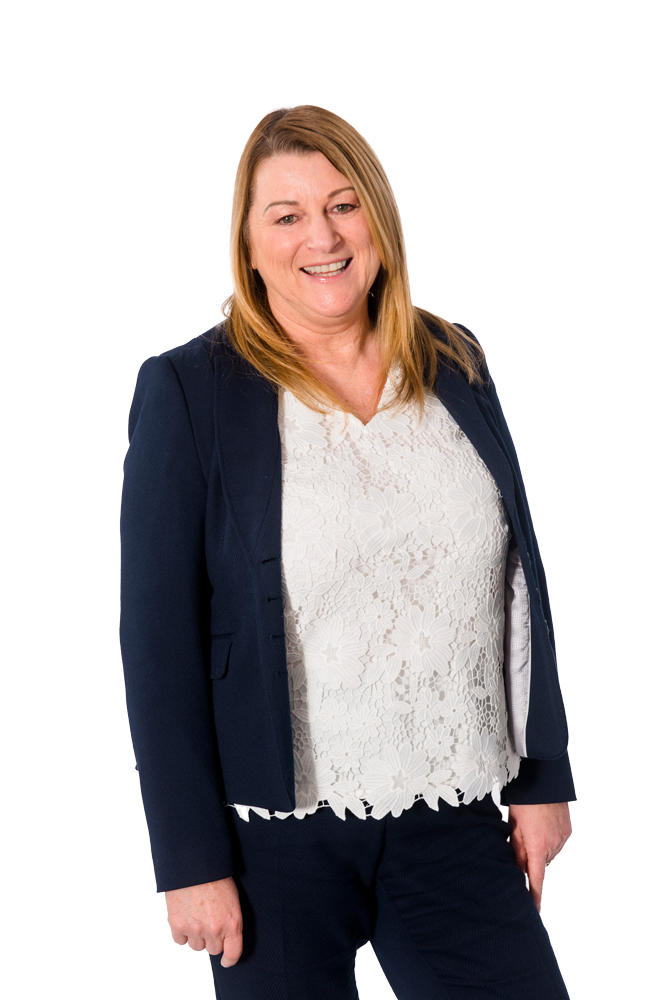